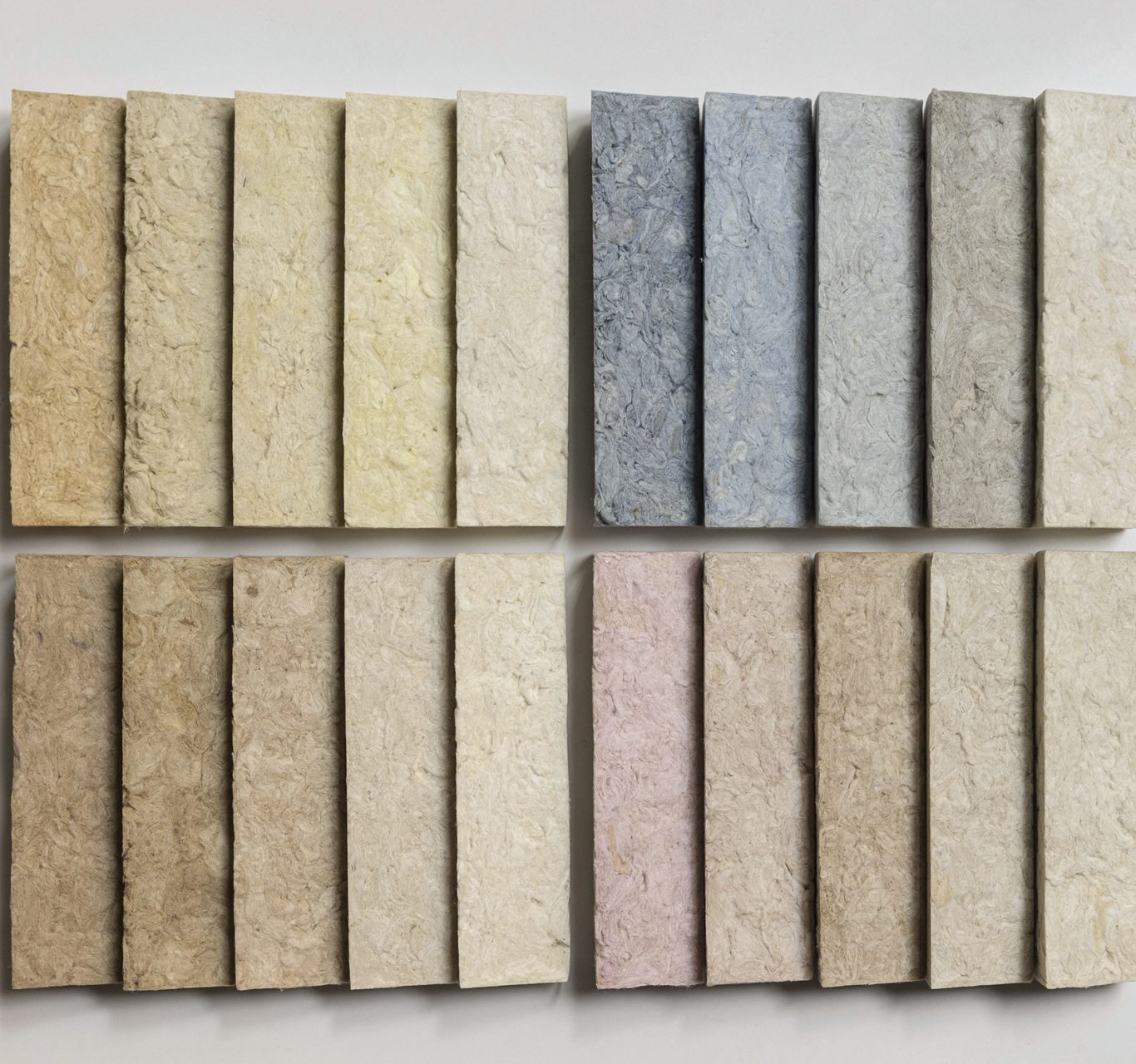

“You need to give it a go many times” – Interview with textile designer and raw material researcher Apol Temesi
The concept of raw material research is just as ambiguous as textile design is evident, despite the fact that raw material focused design is becoming an increasingly relevant field. Certainly, many people have heard of glass concrete, mushroom skin or smart textile. Although such design could be taken as a criticism of other design philosophies and offering experimental alternatives to replace existing products or to restore our relationship to certain raw materials, this is not where Apol Temesi draws the lines of raw material-focused design. We have a responsibility to ensure that the development of a product comes to completion, and that rather than remaining an idealistic, sustainable concept, it is turned into a market-ready product. We talked about beginnings, the challenges presented by the field, recycling possibilities, and last but not least the critical situation the Hungarian wool industry is facing and potential solutions.
At the time you obtained your MA degree, not many people were familiar with the concept of raw material focused design. Even if not completely consciously, but you seem to have sensed that this is a developing area with lots of potential. How did this story begin?
During my university years it started becoming clear to me that I wasn’t going to work in the conventional Hungarian textile industry, because the options are very limited and also because it wasn’t necessarily my way. I was much more interested in finding out how to relate to a sustainable material culture, what to do with textile leftovers, how to break down the material to its components and how to overwrite existing processing methods. In fact this is what lead to my doctoral research, which made me see more clearly that raw material-focused design is a current, contemporaneous field. So much so that in 2014 it was the first publication internationally specifically exploring this subject.
Nowadays this approach seems to be getting traction. HFDA’s incubation programme, for example, which had designers and industry players working in pairs, has recently come to a close. Over a 6-month period, they further developed the Sound Wool concept, which is a soundproofing solution made from wool.
Sound Wool is building on the findings of my doctoral thesis, and we were exploring possibilities for reproducibility and how to work with external companies on a larger scale. The material development process itself took years, resulting in a material with a unique porosity and thickness, as well as superior acoustic properties. In terms of ideal room acoustics, you need several different materials in an indoor space to create acoustic harmony.
So that means wool is a good starting point for this?
Yes, the newly developed material has excellent absorption coefficient at medium and high frequencies. Wool is especially suited to effectively dampen reverberation in meeting spaces, as well as in interior design situations where this type of sound frequency is common. When you enter a meeting space for example, you often feel that it is echoey, sound is bouncing off the various surfaces such as glass, walls and other even surfaces.
So in addition to the decorative aspect, it is also a useful accessory. Would it be possible to achieve the right acoustics using only a couple of square metres?
In an average office meeting space, roughly three square metres are sufficient to adjust room acoustics. You don’t need to cover the entire wall.
Getting back to the subject of the incubation programme: It’s often said that one if not the most crucial moment in the Hungarian creative industries is when designers and industry players find each other. What is your experience?
A designer needs to learn to work together with professionals from other fields. You can’t lock yourself into an ivory tower. You simply have a responsibility to ensure that the development of a product comes to completion, and that rather than remaining an idealistic, sustainable concept, it is turned into a market-ready product. It is vital to be able to communicate in each other’s professional language, understand the problems seemingly remote areas are facing and cooperate. The incubation programme was an attempt at this and it gave me lots of experience. At the same time, you should never assume that you will get the perfect alignment right first time. Material development is also about this: You need to give it a go many times, there will always be new lessons to learn, and realisations that you come to indirectly.
Your MA thesis explored the potential recycling of lorry tarpaulin coverings. Next to PVC, the issue of wool waste appears to be a less critical textile industry problem. How did you go from plastic to wool?
After graduation, I was thinking of leaving Hungary, because the raw material sponsor of my thesis was a German corporation and we considered continuing our work together. I reckon the dilemma whether to stay or leave is shared by many designers. Ultimately, I figured every country has a raw material issue, and it would be a good idea to learn a bit more about it. This is how I came to be interested in this extra segment of sustainable object design, where locality is not restricted to local production and local job creation, but starts at raw material selection.
So that’s how you stumbled upon wool…
I visited a few factories that processed wool. It was clear that there is a huge accumulation of leftover wool from industrial production and so I started exploring various processing methods from a waste perspective. Now, six years later, I have much more insight into why wool depreciated over the past 50 years despite being a premium quality raw material. Today, it is this holistic question that drives me as a designer and that I seek a comprehensive answer to, and professional partners for. Now I see a much bigger potential for this subject. It’s not just industrial leftovers that I focus on but the entire Hungarian wool industry.
Why has wool become worthless? I get the part about waste – I reckon hundreds of kilos are generated that no one uses, but depreciation is not such an obvious conclusion. At least for a layman…
Before, animal farmers in Hungary made a big part of their living selling the wool shorn from the sheep. Today they simply can’t. This is why it would be worthwhile to establish a value creation network ensuring the flow of this raw material to the best possible application areas and using a contemporary approach, and thus also creating jobs.

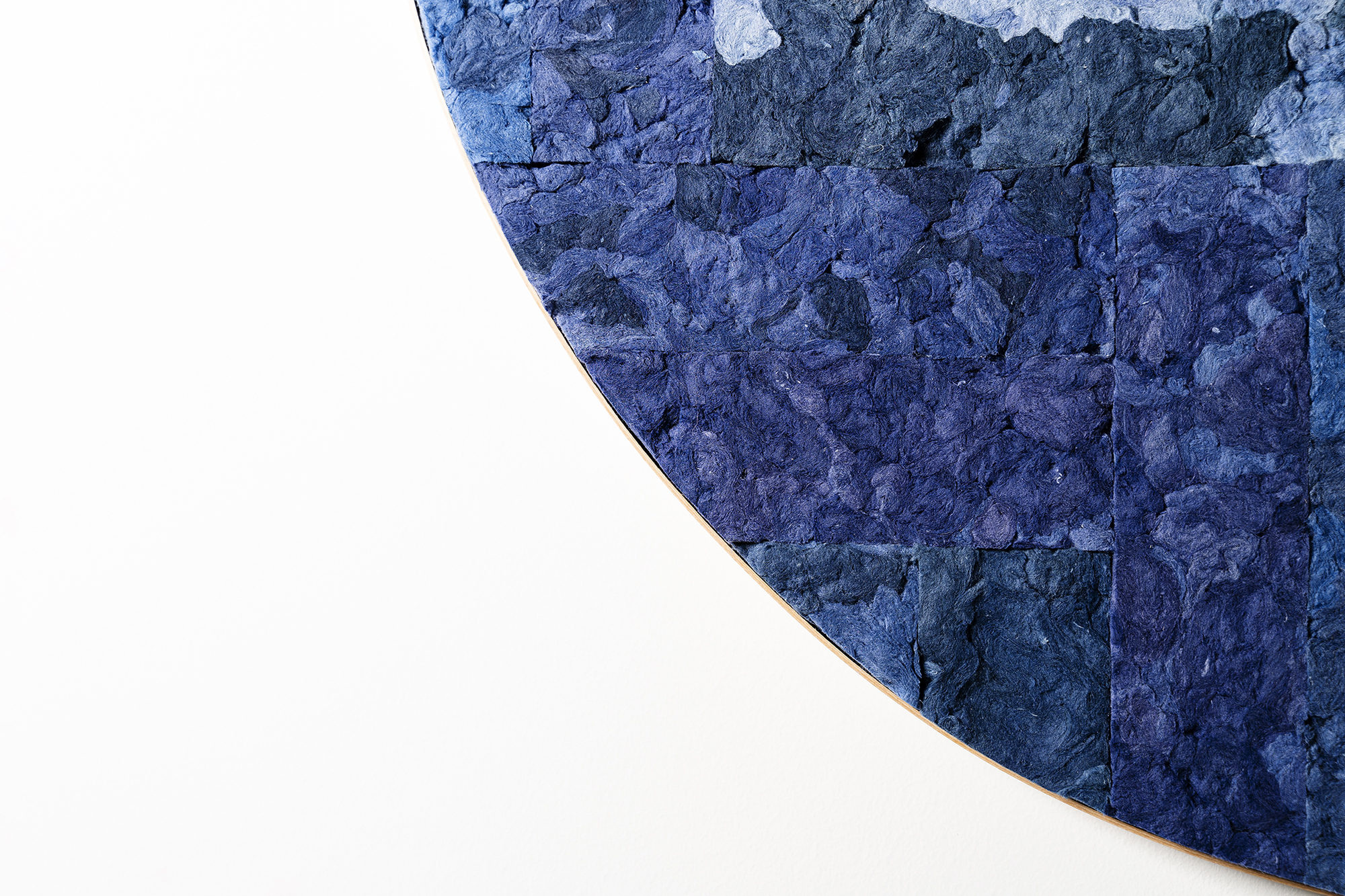
So time for a bit of promotion: why is wool such a great material?
It is a naturally renewable resource. It keeps growing even when you don’t want it to, like human hair. Although there seem to be some misconceptions surrounding it, shearing is in fact beneficial for the sheep, they actually need it. I am also intrigued by the fact that the properties that present major challenges such as a high keratin content or long decomposition time are precisely what make wool flame resistant and give it a market edge in the construction industry which is where I use this material development. But wool holds many more surprises that are not obvious at first, for example, excellent colour fastness, being easy to dye, and also the fact that the procedure I use for processing the material yields a different pattern each time. There are no identical items.
We have already published an interview on material research, covering the alternative use of fungi. To our great surprise, we received a response ultimately praising us for introducing the concept for a new more sustainable or greener material or application method, at the same time criticising us for seldom mentioning what happens to the material being replaced, and how the entire chain is incorporated into the ecosystem. Do you also explore this part of the issue?
I do, so much so that I even covered this in my research, and always start my presentations by saying that raw material focused design always includes two separate avenues. First, there are industrial leftovers that can be considered raw materials, and can be fed back to the cycle, which means waste generation can be stopped. This type of landfill waste accumulation is a huge problem today, and is typically the result of the systemic deficiencies of not planning for the use of the items after the expiry of their lifecycle. And then there is what I call replacement product design. There are natural renewable raw materials that we are not familiar with yet, or we used to be familiar with but are not used any more, including wool. They can be used to replace materials that are currently available on the market but hugely problematic on account of the amount of energy required for their production, being produced from non-renewable energy sources or being harmful to health or non-degradable. Raw material focused developments are specifically designed to put an end to existing waste generation and replace future waste, as well as to override, change, and increase the complexity of, our material use strategies.
I assume that especially when it comes to replacement materials and products, the industry and the market players are often not interested in having changes take place. There is an infrastructure and an established system in place, which allows them to keep their prices so low. Realistically speaking, can these innovative materials fulfil their purpose?
No matter which area of sustainability we look at, whether it’s human ecology, economy or design, we can generally say that at any given time, the combination of two factors can result in change: bottom-up initiatives and coercive external regulations. I’m optimistic because in the field where I work both are present at the same time. There is a bottom-up need from clients and consumers for surrounding ourselves with materials that are not harmful to our health to enable us to take responsibility for our immediate and broader environment to some extent. And also the well-being standard emerging in the construction sector has also become an industry requirement in Hungary. This for example, puts pressure on the industry to pick solutions that meet select sustainability criteria. It’s a slow process but perhaps we are getting better at formulating how to develop more humane and coordinated products.

You’ve mentioned that it’s not only material development but also wool and the current situation of the wool industry that are close to your heart. In the distant future, when can you say your work has borne fruits?
First, I’d like to take wool-related product developments to the next level, where animal farmers, the sectors and the market can be linked through the development of niche products. Wool is valuable and with the help of contemporary product developments it could meet all construction industry requirements. If this was realised in Hungary, the players could be linked from the materials all the way to the markets, the model could be adopted in other countries too, where wool is also a locally produced raw materials.
If this the desired scale, perhaps it’s not excessive to ask whether raw material focused design will become one of the relevant topics in the next ten years.
I hope it will. Clearly in Western Europe, and apparently increasingly so here in Hungary.

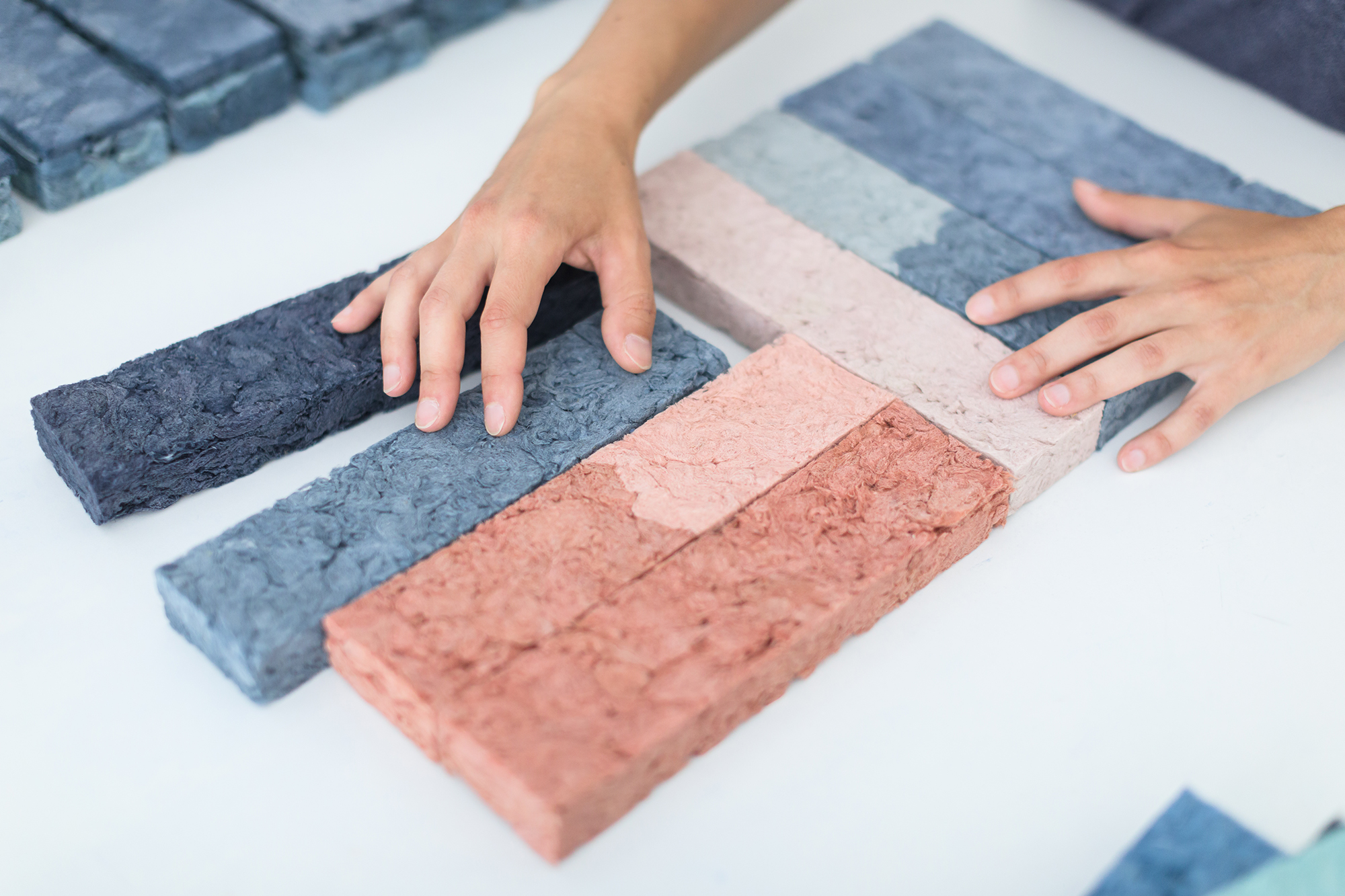
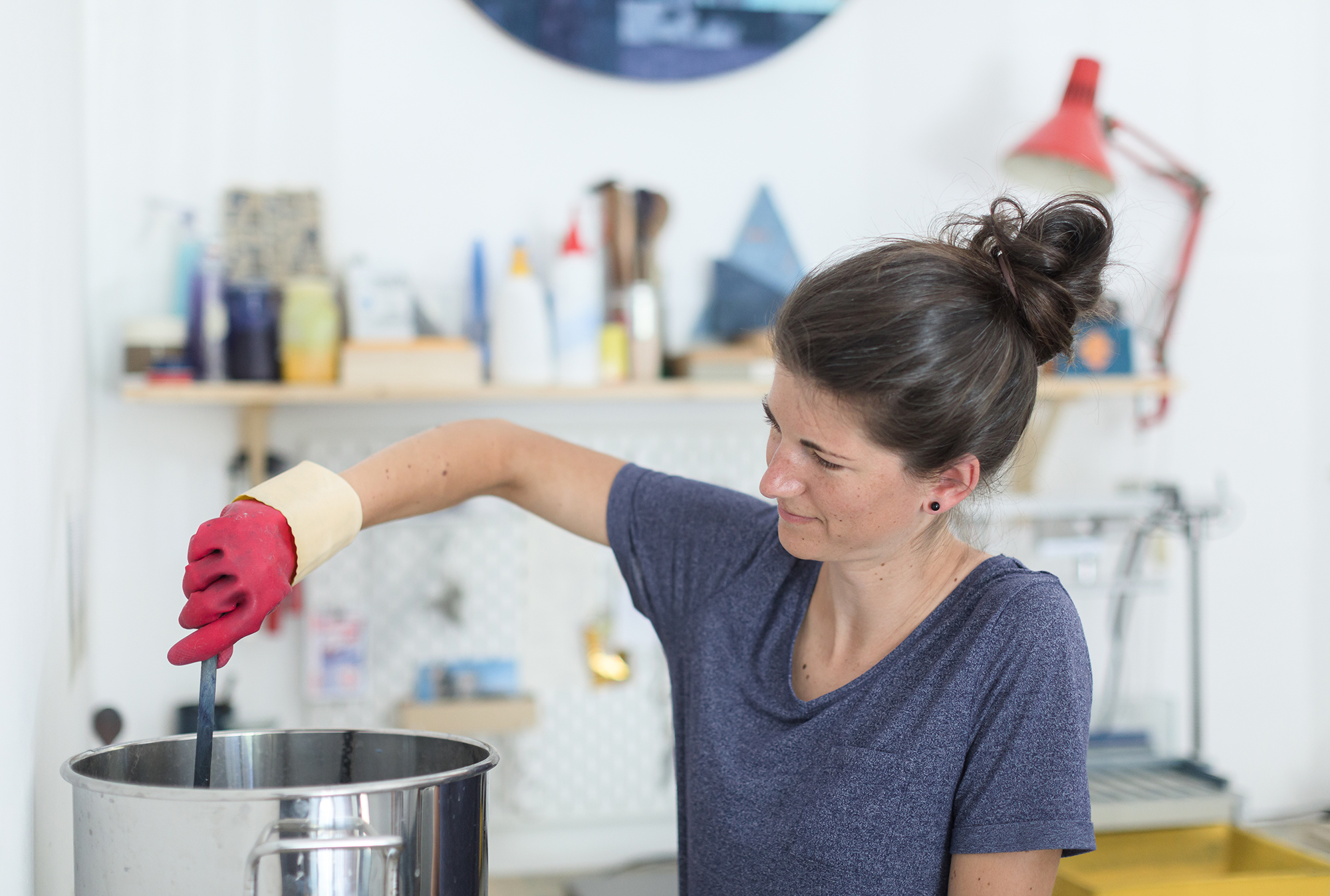
// /
Photo: Balázs Mohai